We work around the clock
to solve real business problems
We demonstrate our concern about the environment through innovative product design which minimizes the impact on the environment. Sustainability is embedded in product design and manufacturing, and includes:
-- Reduction of carbon emission during manufacturing as well as throughout the product life-cycle
-- Ability of our products to sustain extreme environmental and weather conditions
-- Compliance to RoHS (Restriction of Hazardous Substances Directive)
-- Extended product life
-- Development of biodegradable products
-- Usage of recycled raw material as inputs
-- Engagement with supply chain partners for reduction of embedded carbon
• First Indian manufacturer to produce MVCC, which ensures no faults with short duration touching of phase conductors during wind conditions.
• Insulated by a covering made of specialty polymer insulating material(s) as protection against accidental contacts with grounded parts such as tree branches etc.
• Such covered conductors reduce interruptions by contact of tree branches or creepers, cause negligible leakage current on surface, provide increased safety in high density populated locations, protect big birds and animals like peacocks, flamingos, elephants etc., increase the power distribution network reliability, reduce power interruptions and outages.
We have innovated special technologically advanced PV wire for Solar Industry which serves the following challenges-
(a) zero transmission loss (b) life expectancy beyond 25 years (c) fire retardant (d) RoHS compliant (e) UV resistant, and (f) anti rodent & anti termite
Electron beam cross-link technology enables us to enhance insulation material performance by changing thermoplastic material to thermoset. Our four irradiation units are capable of cross-linking wire from 0.2 sq mm to 400 sq mm and cables with diameter upto 60 mm.
Apart from other cross-linking technologies, irradiation cross-link products are easy to cut and strip.
Irradiation benefits & features
- ✓ Higher temperature resistance
- ✓ Increased product life
- ✓ Thermoset (melt resistant)
- ✓ Increased mechanical strength
- ✓ Increased abrasion and cut through resistance
- ✓ Increased chemical and oil resistance
- ✓ Increased crush resistance
- ✓ Increased shear and compressive strength
AL59 conductors are made out of Al-Mg-Si low resistance high conductivity alloy with excellent electrical characteristics, excellent sag-tension characteristics and superior corrosion resistance to that of ACSR (Aluminium Conductor Steel-Reinforced). As compared to ACSR they have lighter weight, comparable strength and current carrying capacity.
The metallurgy and manufacturing of AL59 requires energy intensive processes for precipitation of SiMg2 phase. This involved multiple heat treatment processes to achieve consistency in parameters and manufacture first time right material.
With the consistent R&D efforts, thorough analysis and setting up the stringent process norms followed by several trials on various wire sizes, APAR team succeeded in achieving the desired wire parameters as per the technical specification by redefining the recipe which did not require the drawn wire to be heat treated thereby providing the following benefits :
• Improving the productivity
• Saving of electricity 13.75 units/ MT
• Material saving
• These have higher current carrying capacity (CCC) compared to conventional ACSR or AAAC, and thereby upgrade transmission networks with minimal infrastructural impact.
• These are more energy efficient for power transmission as they generally have lower resistance (lower I2R losses).
The overhead bare aluminum or aluminum alloy conductor is subject to various exposures like heat, moisture, rain, pollutants over its service life. At coastal areas it also has exposure to salty air.
Protective compound (grease) application in overhead transmission conductors are used to prevent moisture, direct ingress of water and pollutants at interstices between the layers and wires.
The application of grease and minimum weight is directed by the applicable standards. However, in the actual usage/ application, the amount of grease applied on the conductor had high variations.
To provide consistent grease application in conductor as per applicable specification, APAR team designed and developed motorized grease applicator with pneumatic control which successfully facilitated grease application in conductor at controlled rate and weight at each cage of stranding machine. This innovation resulted in waste reduction and consistency in the quality of product.
We produce dull finish conductor (to reduce the reflection of conductor surface due to aluminium lustre) which offers following benefits:
• The surface emissivity increases from 0.23 to approx. 0.42
• Improvement in current carrying capacity by 5%
• Suitable for V, HV and EHV overhead, long distance transmission and distribution lines
• Can be installed within the vicinity of airport as dull finish conductors eliminates the light scattering from conductors surface
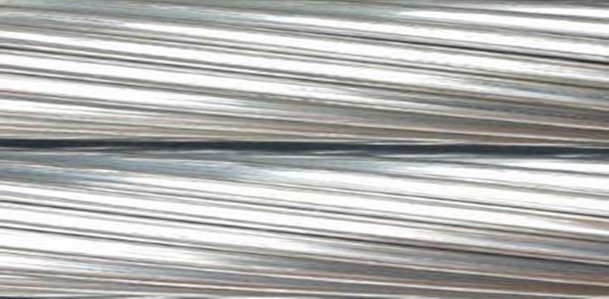
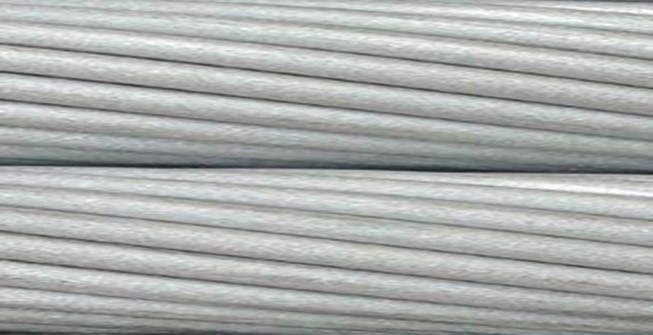
APAR is 1st company in India to obtain a VDA license which is used in the Selective Catalytic Reduction (SCR) system of vehicles to convert the NO2 emissions to nitrogen enabling vehicles to conform to BS6 emission norms.
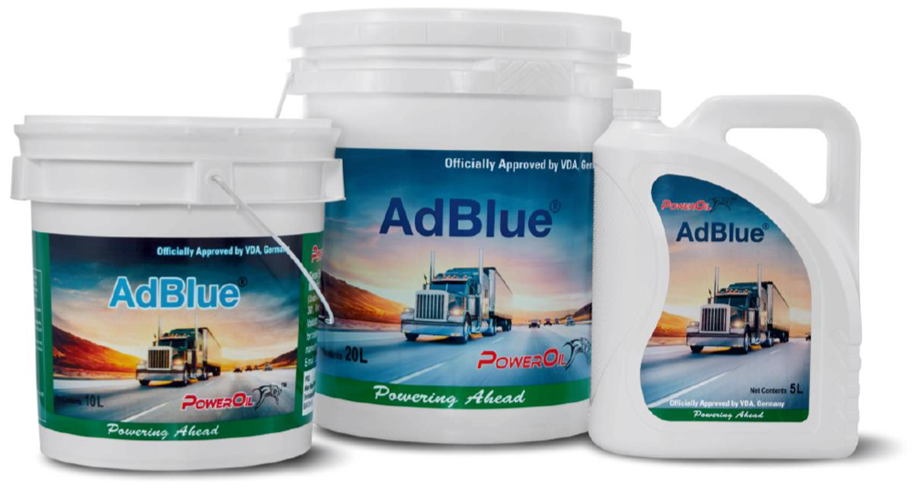